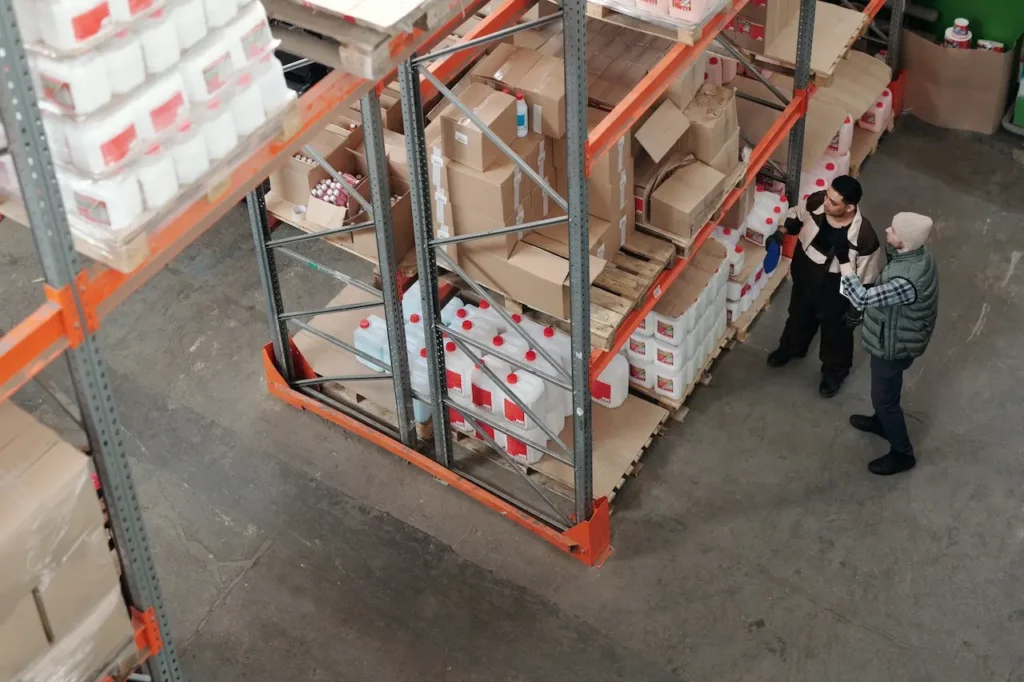
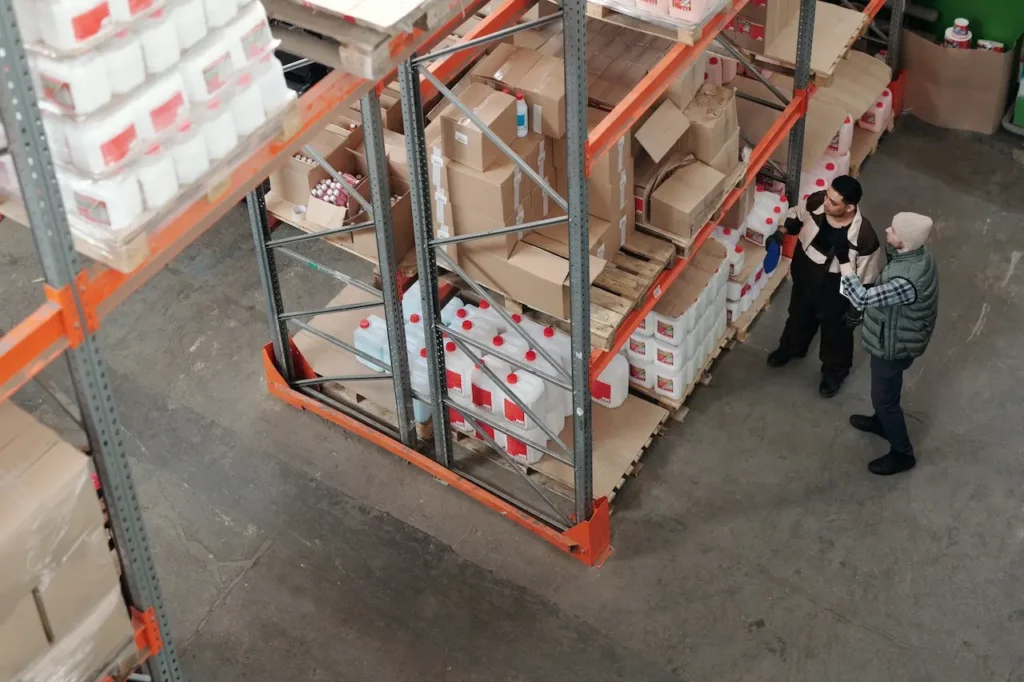
8 Best Practices for Efficient Inventory Management | Image source: Pexels
Maintaining control over the inventory of items is crucial to ensuring a healthy sales volume and, consequently, reducing operating costs. But despite its significance for the outcomes, managers don’t always give it the attention it deserves.
In light of this, we will discuss the 8 best practices for efficient inventory management in the following subjects so as not to harm your company. Continue reading to learn more!
1. Keep track of entries and exits
One of the most important inventory management mistakes a company can make is failing to properly record inputs and outputs. You never have a precise count of the items that are available since you have no control over anything that goes in and out.
It also makes it more difficult to keep track of when things need to be replaced, raising the possibility of shortages or surpluses. Make a note of every movement you make to avoid these issues.
In this instance, it is also important to keep in mind the significance of regulating inputs and outputs that are related to the exchange and return procedures in order to ensure total accuracy in the monitoring.
2. Keep a check on product turnover
The amount of time each item is kept in stock before it needs to be renewed is known as material turnover. We refer to an item as having a high turnover when there are numerous deliveries each week due to the high output volume.
Monitoring this indicator is essential to determine when to contact the supplier in order to avoid supply shortages.
Low turnover items, on the other hand, show that those things are not sold, therefore it is best to avoid buying them, spread out purchases over time, or buy them in lesser quantities.
But for this task, keeping track of inputs, outputs, and the number of days until output is crucial.
3. Don’t allow too much or too little stock
Lack of control over product movements causes shortages and an excessive amount of inventory. This happens when turnover and item quantities are not monitored, which leaves the purchasing sector in the dark about what needs to be done in terms of acquisitions.
These faults affect the company’s financial performance since they raise expenses, increase the likelihood of losses and waste, and undermine sales when there is a shortage of products but a high demand.
The rate of shortages and excesses is ultimately significantly reduced by finding solutions to the issues of managing inputs and outputs and the rotation of materials.
Read also: Everything You Need to Know About Inventory Management
4. Take inventory of materials
The material inventory entails counting the things that are on hand and comparing the quantities on hand with the data recorded in the utilized controls.
The database is continuously updated using this manner. This lowers the possibility of stock holes and raises the quality of the information provided to the buying sector.
The optimal way to ensure that the physical inventory x accounting inventory balance is as precise as possible is to consider groups of items at a time when you do this balance, leaving the general inventory to be completed annually or as frequently as the manager considers necessary.
5. Have a database of standardized items
Errors and duplicate entries are possible because there is no standard for the registration of materials.
When doing this, the seller runs the danger of losing control over the stock and being unable to determine if the product “x” is actually out of stock or if it has just been recorded in another manner.
In addition to utilizing one code and description for each type of item, this issue has to be resolved by defining a common method for code and description creation.
6. Integrate the stock sector with other areas
As you can see, inventory data is essential for the efficient operation of both purchasing and sales. One of the biggest faults in inventory management is not investing in information sharing and neglecting to combine these areas.
Sharing information and maintaining open lines of communication is the best way to avoid this issue and guarantee effective inventory management. Additionally, most businesses are hesitant to spend money on an integrated inventory management system that streamlines data sharing and automates these processes.
7. Do not manage inventory manually
It is of the utmost importance to invest in technology due to the volume of data generated during a stock routine and the requirement to monitor and control information.
Therefore, permitting operations to be carried out manually raises the possibility of errors, jeopardizes productivity, and reduces the security and dependability of information.
Adopting an inventory management system has several benefits, including reducing costs, allowing staff to play a more strategic role rather than a solely operational one, and facilitating decision-making.
8. Organize your stock
It is not a good idea to leave tumultuous goods in one sector with no room for its staff to move around as this causes the sector to suffer significant losses in addition to being an obvious indicator of disorder.
Here are some extra pointers to prevent stock losses:
- Ensure that there is space in the inventory for staff to move around;
- Sort items by department;
- Maintain a tidy and clean inventory;
- Put up signs in each section to understand where to find each product;
- Keep the area open;
- Take precautions to avoid the appearance of mice or insects.
Lastly, in order to maintain the optimal size of your stock, it is important to specify the maximum and minimum stock of each product. Despite the fact that we are aware of how complex this action is, we can make it more efficient and pleasant by using the right tool.