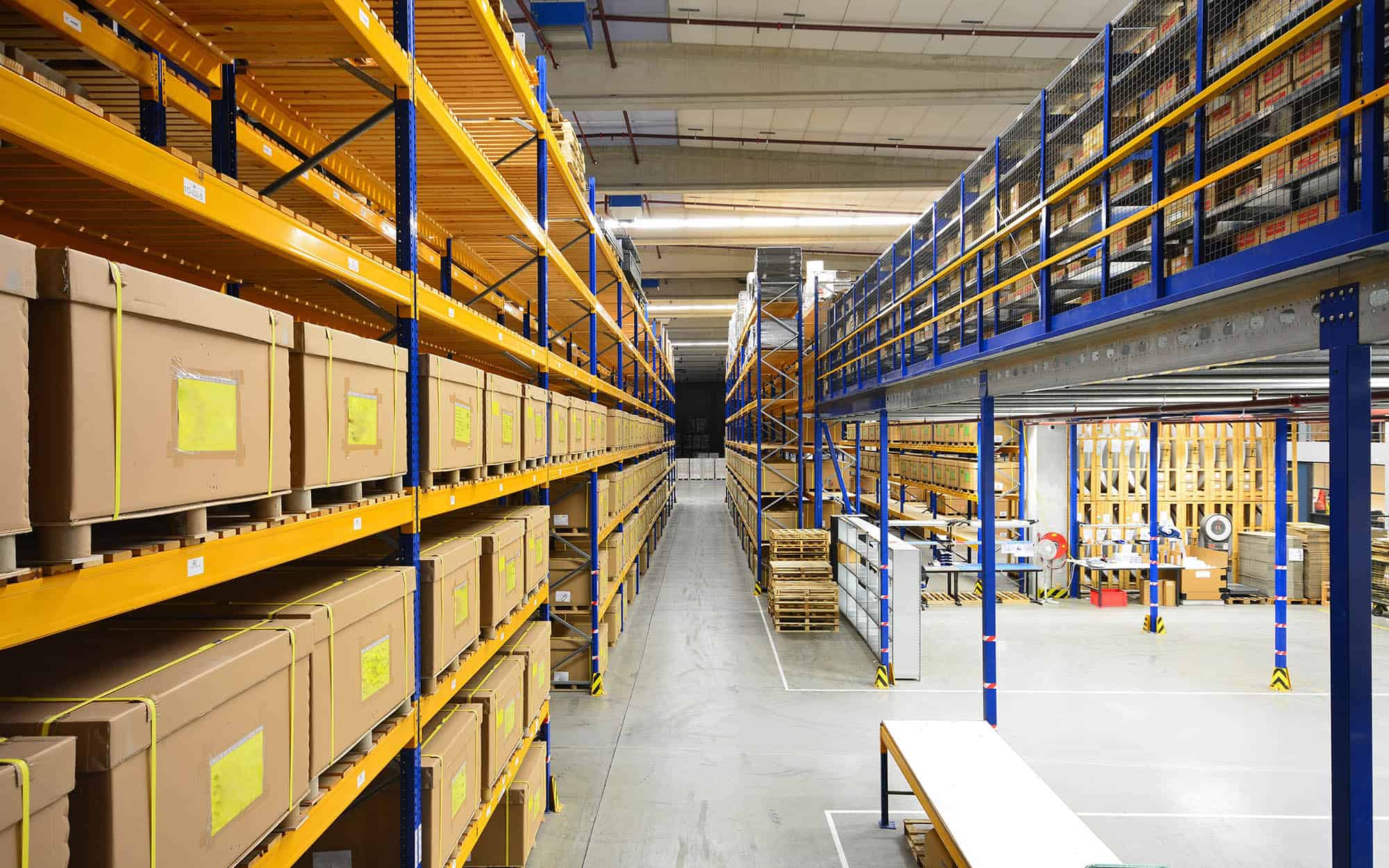
The order fulfillment process is complex, and in the world of e-commerce, accuracy means everything. While mistakes are bound to happen, repeatedly failing to meet customer standards can create the perfect recipe for disaster.To reduce the likelihood of unfulfilled orders, start making serious changes to your order-picking system. With the oversight of a logistics service provider like FW Logistics, you can take your customer satisfaction levels higher than ever before.
Where Order Accuracy Goes Wrong
Order accuracy is one of the most important metrics companies should test. However, far too many people underestimate everything that goes into preparing these orders—and what could quickly go wrong, such as an incorrect item, misshipment, or incorrect unit quantity. Eventually, neglecting these common issues causes dissatisfied customers and hurts your bottom line.
How Fulfillment Center Warehouse Picking Systems Can Help
The order fulfillment process has so many moving parts, and a warehouse fulfillment center is one the most stress-free ways to gain control over your deliveries. With this option, you can get advice on the right order-picking strategies, tips on properly organizing your warehouse or fulfillment center, and even feedback from more experienced pickers.
Our warehouse fulfillment solutions are more hands-on than ever before. See how we’ll serve as a direct extension of your business.
Our Top-Notch Fulfillment Solutions
Four Starter Tips for Warehouse Order Picking
Start revamping your order-picking strategy and improving accuracy with the following tips:
-
Quantify Your Accuracy Rate
As important as your order accuracy rate is, many people fail to adequately measure it as a key metric. As such, they often don’t have a clue whether this rate is improving or showing signs of a much larger problem. By starting with a simple measurement system, your company can fully visualize its logistical performance.
-
Set Your Accuracy Rate Goals
After properly tracking your accuracy rate and gaining a sense of direction, you can now set goals to improve this number. Combined with a realistic timeframe and a collaborative team, you can then delegate responsibilities to each employee.
-
Focus on the Picking and Packing Process
The pick-and-pack process is the most common aspect of the fulfillment process where errors occur. Any commerce team making room for accuracy improvements should be especially tuned into what can be better automated or optimized in this area. Even something as simple as using the correct barcodes or choosing the right colors could have a significant impact.
-
Use the Best Technology
Another perk of outsourced fulfillment centers is the incredible technology they bring to improve accuracy. These warehouse management systems were created from the efforts of hundreds of people who’ve seen the same issues time and time again. As such, these systems are designed to focus on speed, accuracy, and reducing the necessary manual work to fulfill an order.
Keep Your Operations Running at Their Fullest Potential With FW Logistics
At FW Logistics, we’ve seen it all. We know that for your workflow to align with your goals, you need real, long-term solutions that won’t cut corners. When your fulfillment services aren’t up to par, we can return them to where they belong.