When optimizing the picking process in a warehouse, it is important to recognize two key concepts. First, no one strategy or technology fits every case. Second, effectively improving warehouse operations requires data collection, process improvement, and technology.
Click Here: Optimize Your Picking Process With This Advanced and Affordable WMS
As a best practice, warehouse managers should conduct an ABC analysis, properly document and review the current process to detect inefficiencies, and improve warehouse processes before introducing any form of warehouse automation and/or warehouse technology. For effective optimization of the picking process, a warehouse manager must match the correct picking and warehouse automation strategy with the goods being handled (e.g., full pallets, full cases, individual units, cargo).
So, let’s dig into the steps needed to optimize one of the six primary warehouse processes.
1. Conduct ABC Analysis/Order Profiling
To efficiently manage inventory, the first step is to gather data and understand how we currently handle it. One effective way to do this is by conducting an ABC analysis and/or order profiling.
An ABC Analysis enables a warehouse manager to categorize inventory into three groups (ABC) based on order volume. The goal is to arrange inventory so that the highest-volume items (A) are stored at the front of the warehouse, while the lowest-volume items (C) are placed toward the back. This results in less time spent walking and fewer man-hours needed to complete picking operations.
The image shows a warehouse with high-volume inventory (RED) spread out, resulting in unnecessary walking time. After the analysis, we moved high-volume items (RED) to the front and low-volume items (GREEN) to the back.
Warehouses and distribution centers that do not process customer orders can conduct an ABC analysis based on receiving and shipping volumes.
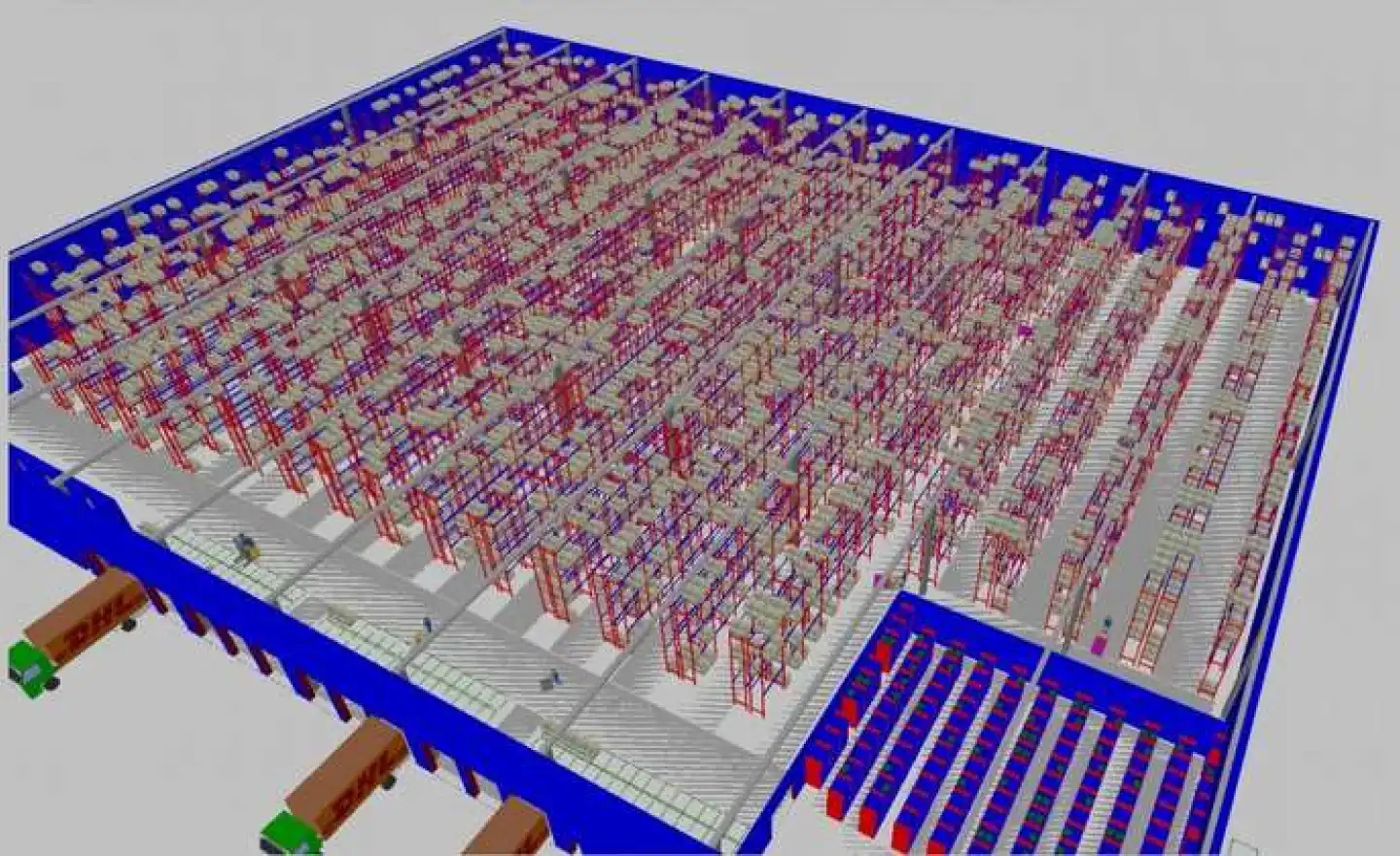
Before ABC Analysis
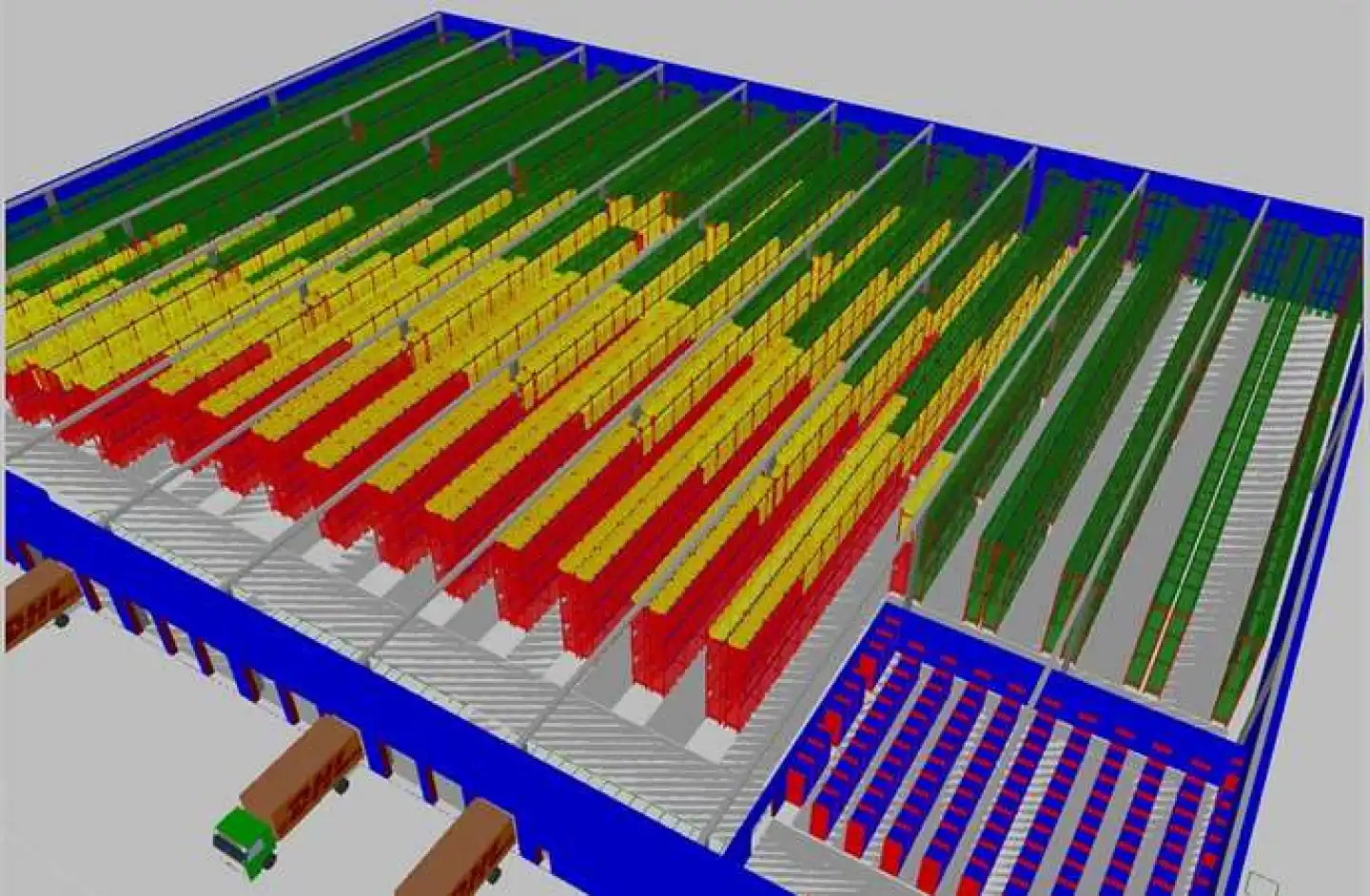
After ABC Analysis
2. Select the Correct Picking Methodology
When picking, a warehouse manager must also consider the methodology to adopt. While most operations still rely on the Pick-to-Order approach (one of the most inefficient approaches to picking), some methodologies can be implemented to significantly improve and increase warehouse efficiency.
The goal here is to apply one picking methodology or a combination of methodologies to reduce travel time between pick locations.
Depending on the operation, movement between pick locations can account for up to 50% of a picker’s time.
In the Picker-to-Goods method, the picker travels to the location where the goods are stored after being assigned to an order (or part of an order). Then, the picker collects the item and delivers it to the dispatcher to prepare the goods for shipping.
The following are the most common Picker-to-Goods methods used in today’s warehouses and DCs.
Picker-to-Order/Piece Picking
In the Picker-to-Order method, the picker collects all items related to an order. The picker travels to the locations where the goods are stored with a detailed list of the items to be collected and proceeds to pick up the entire order.
This approach is only effective with orders with a low number of SKUs/items. Processing orders one at a time increases the order accuracy rate and reduces cargo handling as goods are moved from storage to shipping in one step.
The downside of this approach is that it is inefficient and inaccurate for orders with more than one item/SKU. As the number of SKUs/items per order increases, the number of errors increases.
Cluster Picking
Cluster Picking is more efficient than Pick-to-Order because it allows pickers to collect multiple orders simultaneously.
In this method, the system provides a picking list to the picker with the most efficient route to pick multiple items simultaneously. As the clerk collects individual item orders, items are separated into bin partitions to reduce/eliminate order errors.
Most warehouse management systems (WMS) capable of supporting Cluster Picking can also prioritize item picking if one set of orders needs to be given priority over another.
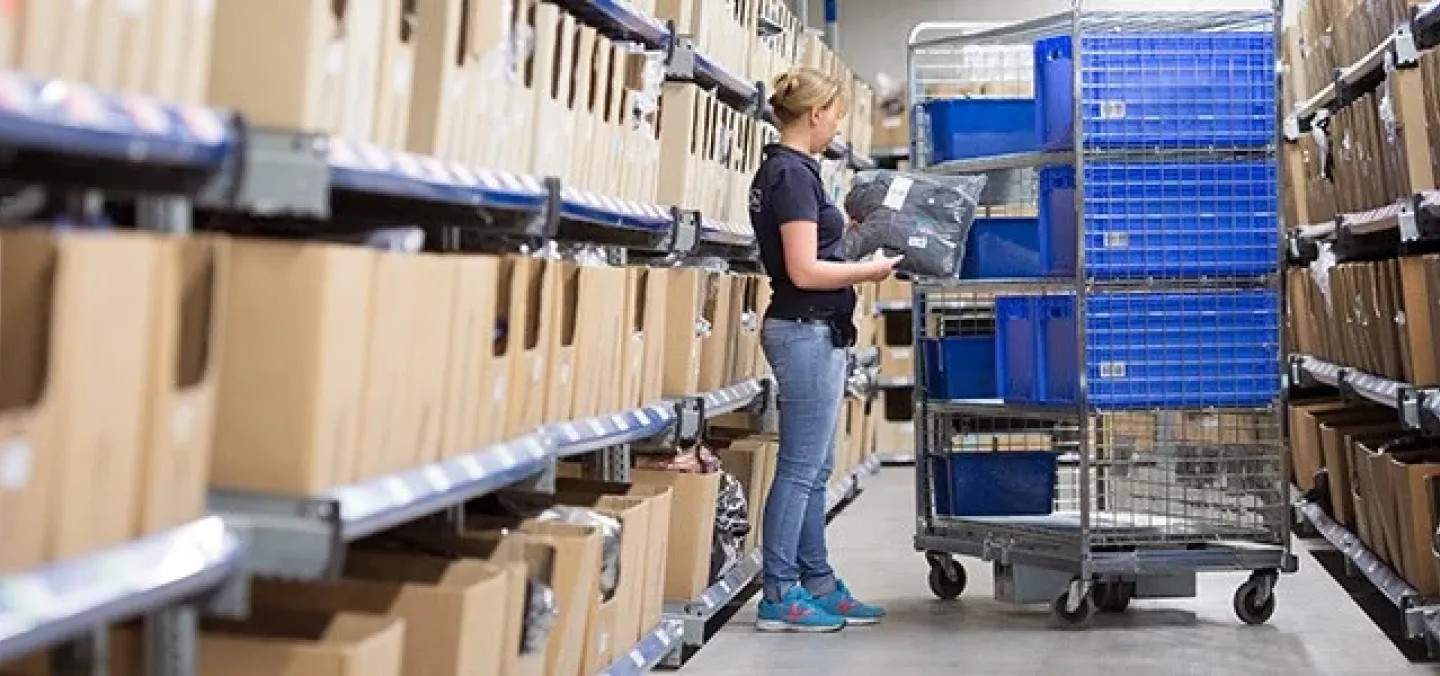
Example of Cluster Picking
Zone Picking
In Zone Picking, the warehouse divides SKUs/items across multiple zones and assigns specific zones to dedicated pickers.
Trolleys, cages, pallets, and/or conveyors transport orders from one zone to another. When an order contains more than one Stock Keeping Unit (SKU), specialized pickers in each zone fulfill the multiple picking lists assigned to them.
The specialization of pickers in zones and the SKU-location knowledge they acquire, combined with the ability to fulfill multiple orders simultaneously, significantly increase the speed and effectiveness of the picking process.
Warehouses and distribution centers that process a large number of SKUs and handle multiple orders best utilize zone picking.
Wave Picking
In Wave Picking, we group orders and release them to pickers at specific times during the day and across different zones, depending on the time required to pick the orders. This aligns the picking process with specific events such as shipping schedules, replenishment cycles, shift changes, available workforce, etc.
A warehouse management system that supports Wave Picking manages Wave Picking more effectively. In this case, the WMS releases sequential orders throughout the day depending on specific criteria.
One advantage of Wave Picking is that it helps reduce each picker’s workload variation by allowing the picker to focus on executing a specific task (case picking, packing, repack picking, etc.) on each Wave Pick.
46% of best-in-class companies are more likely than others to use advanced pick methodologies.
3. Introducing Technology
We have covered two fundamental approaches to optimizing the picking process. Now, it’s time to introduce the technology aspect.
Barcode Scanners
Barcode scanners are one of the simplest but most effective ways to improve warehouse operations. They allow us to identify products, locations, and containers more effectively.
Using a combination of barcode scanners and picking lists, warehouse clerks can confirm they are picking the right product for the right customers from the right locations. This warehouse technology allows for faster and near-error-free data collection and product validation.
On average, the technology error rate when using barcode scanners is 1 in 3 million.
Wearable Computers
Wearable Computers are another warehouse technology that can have a significant impact on improving warehouse processes.
Wearable computers provide a small screen and keyboard that allow pickers to interact with the WMS from anywhere in the warehouse in real time. In some cases, these devices provide the capability of a finger-mounted device to provide barcode scanning capabilities. See below:
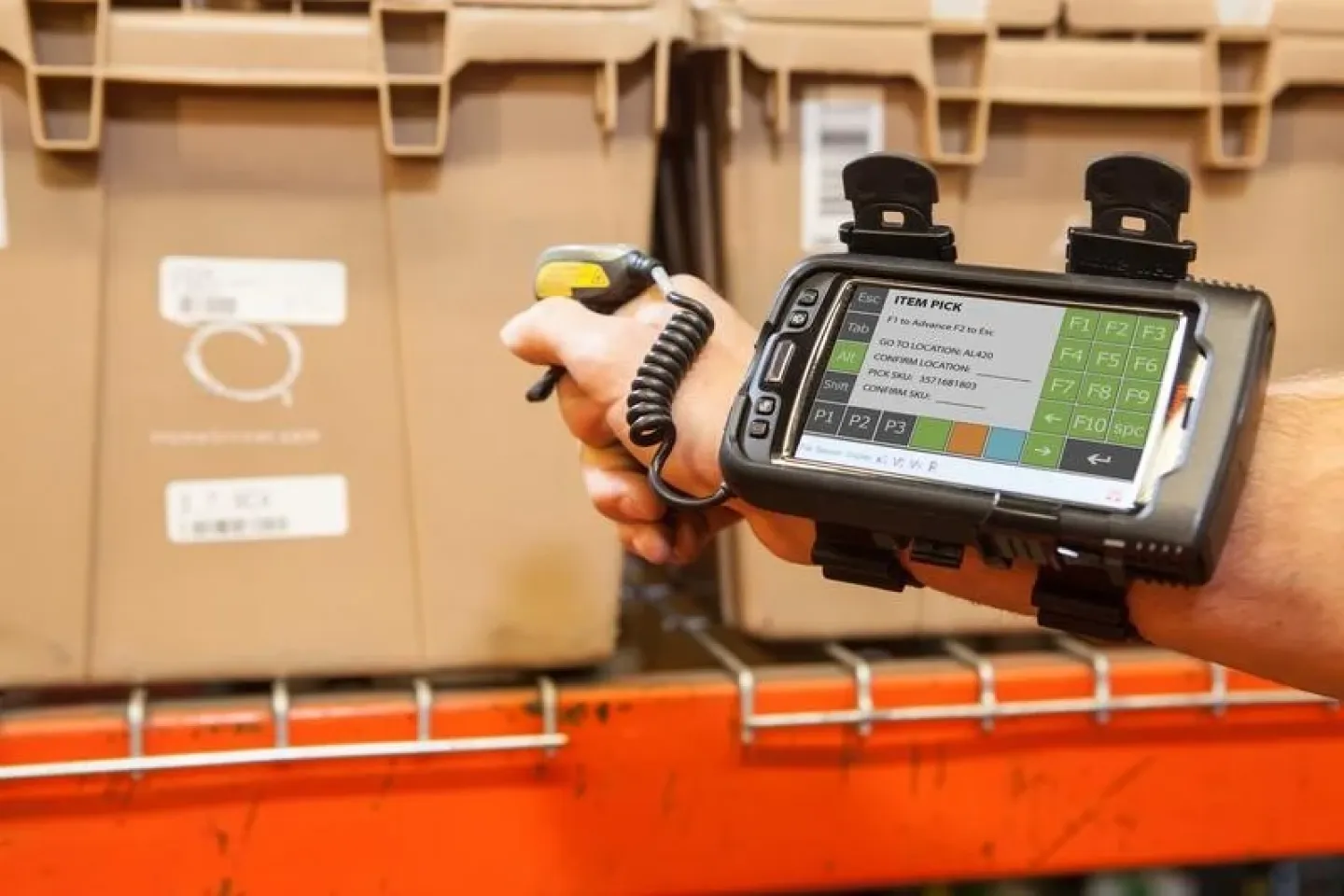
Example of Wearables
The wearable aspect of this technology leaves pickers with both hands free to handle cargo, significantly reducing the likelihood of accidents and product damage.
Before adopting any wearable solution, decision-makers must confirm with their WMS vendor that their software is compatible with the desired wearable computer.
Voice Picking
Voice Picking is highly efficient and effective. With voice picking, operators have a headset and microphone directly connected to the WMS over local wireless warehouse networks.
During the picking process, the operator also interacts with the WMS via voice commands, and the system provides verbal instructions regarding the place, product, and quantities that he/she needs to pick.
Some of the most significant benefits include, but are not limited to:
- Increased accuracy & productivity
- Multi-language capabilities
- Reduction of data entry errors
- Improved safety through hand- and eye-free technology operation
- Increase availability of picker time
More advanced (and expensive) technologies, such as Pick by Light, RFID, and Wearable Glasses, can considerably increase efficiency. However, the technologies described above offer solutions that are both affordable and accessible while yielding great results.
It’s crucial to collect and analyze data, and review and improve existing processes. Introduce the right technology in the right places. Neglecting any of these steps could lead to a diminished return on investment, loss of capital, and wasted time.
To learn more about the different warehouse processes and how to optimize them, click here.
If you are ready to find a solution to optimize your picking process or any other warehouse process, go to our Solutions Finder tool.
If you want to learn more about warehouse digitalization and optimizing warehouse processes, you can follow us on LinkedIn, YouTube, X, or Facebook. If you have other inquiries or suggestions, please contact us here. We’ll be happy to hear from you.