Disruptions in the Supply Chain Affect the Automotive Industry
13th May 2024
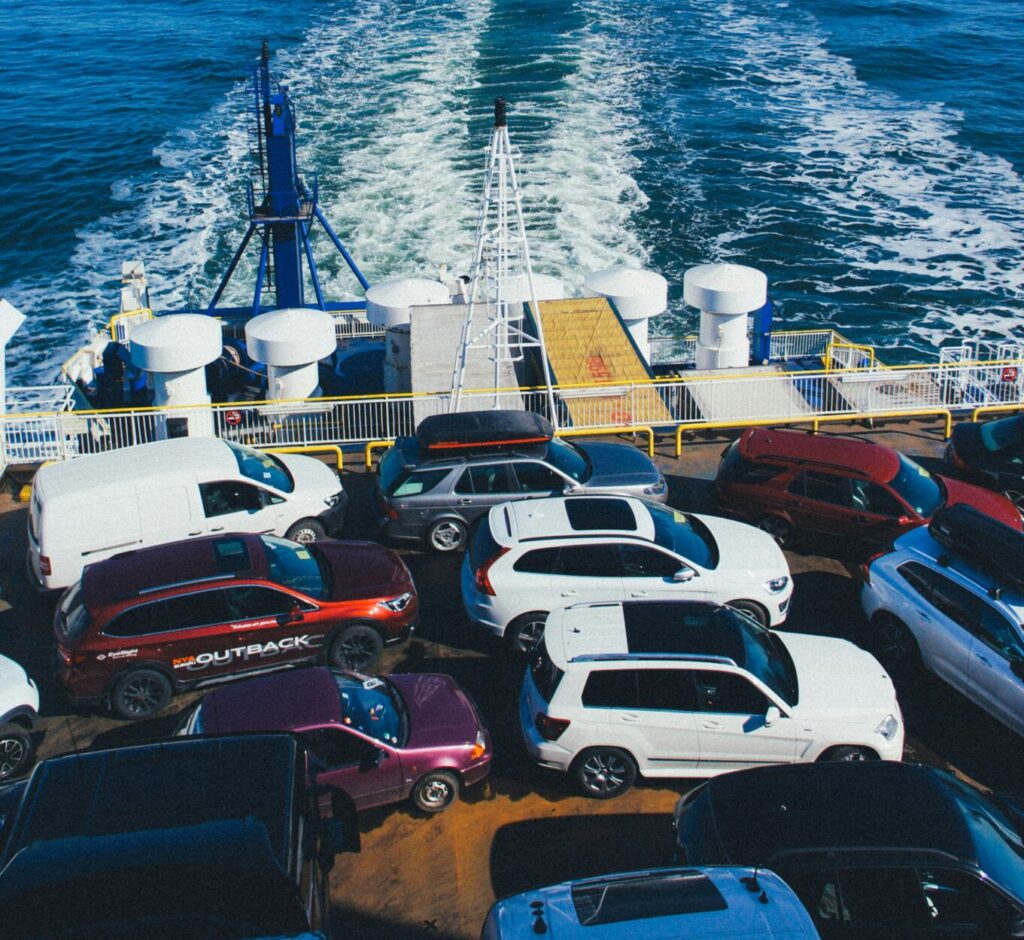
The automotive industry’s reliance on its supply chain running smoothly is important to ensure the consistent production of vehicles for consumer and corporate demand, especially considering that most vehicles can contain between 15,000 and 25,000 component parts.
Chris Thompson, Operations Director at Electrix International, a global supplier of stainless steel electrical enclosures, has offered some expert insight into the supply chain issues facing the automotive industry, including the impacts it has and posing some potential solutions.
Reduction in workforce
One significant concern in the automotive industry is the significant shortage of laborers and workforce. In fact, an ABB survey of around 600 global industry experts found that skills shortages of talented laborers were of the greatest concern in North America, with 56% of experts outlining it as a problem. 48% also stated that new skills were required to adjust to the fast-changing landscape of the industry, with more needing to be done to attract people to join the industry.
Technology shortage
One significant issue within the automotive supply chain is the shortage of key technological components, like semiconductors, that go into vehicle production. These inventory shortages increase delivery lead times, and the scarcity of parts has forced manufacturers to raise costs, meaning final prices for consumers are even higher than before.
In fact, the cost of a new car in 2024 is now an average of $48,759, which could increase further should these delays increase. Not only does this have an impact on new car purchases but also on the aftermarket industry, as it affects repair and maintenance services being unable to work on vehicles with replacement parts.
Geopolitical and naturally occurring phenomena
It’s not just physical issues that can affect the supply chain, as the wider landscape of the world can have a huge impact on the automotive industry. Geopolitical developments that automotive manufacturers have no control over can cause interruptions in the flow of goods and materials. For instance, Volvo and Tesla had to suspend manufacturing due to the conflict in the Red Sea in early 2024. Conflicts and tensions between countries affect trade and tariffs placed on materials like steel and aluminum, which in turn raises costs for manufacturers. The knock-on effects can have huge implications in the long term.
In addition to geopolitical situations, naturally occurring phenomena and disasters can also contribute to production and supply chain issues for the industry. Whether it’s hurricanes, wildfires, or earthquakes, they’re unpredictable in their very nature and can be hugely disruptive to production facilities and transport networks. The knock-on effect leads directly to supply shortages and delays in production.
How does the industry respond to these challenges?
The automotive industry has been forced to create and implement strategies to deal with these challenges, with one solution being to diversify supply chains, which involves reducing their reliance on single-source suppliers. This means establishing strategic partnerships with multiple suppliers, as well as investing in localized production facilities, and making the most of emerging technologies to streamline and optimize operations.
This creates more flexibility in managing the supply chain to react quickly to the impact of disruptions and continuing with processes despite unforeseen circumstances. The market and industry are constantly evolving, so staying on the cusp of new strategies can avoid major disruptions.
Disruptions within the supply chain have emerged as a significant challenge for the automotive industry, whether it’s geopolitical tensions or natural disasters. The challenges posed to the market have impacted everything from the production of new vehicles to increased costs of units to materials and affecting consumer demand. This is why it’s so crucial for the industry to explore proactive solutions to mitigate these risks and build a stronger risk management strategy.
read more