In the phase before the products reach the store, IKEA distribution service makes sure all goods are transported from suppliers to stores. However, once in the stores, logistics handles the off-loading and arrangement of goods.

IKEA was founded in 1943, in Sweden. IKEA focused on offering a wide range of good quality, stylish, well-designed, and functional furniture at a low cost so that more people could afford it. IKEA kept cost reduction at the center of any decision making. It made efforts to improve its internal supply chain processes like packaging, warehousing, and transportation which contributed to its cost cutting objective.
IKEA’s supply chain management became the key factor for the success of the company. As a result, IKEA managed its costs better than its competitors and could offer products at 30% lower costs. Nowadays, we can say that IKEA is expanded around the world, by the year 1990, it had 89 stores in 21 countries, and it was operating 260 stores in 36 countries in 2008. At IKEA, thousands of products are handled daily. The movement of goods must be as efficient as possible, under all circumstances, guaranteeing service to our customers and ensuring that the products they seek are always available to buy. Jobs in logistics account for about 20 -25% of each store’s co-workers, all of whom
provide a vital link in our operations. Our goal is to be in full control of the space and the volumes of goods in order to maintain uninterrupted sales.
The sheer volume of goods coming in and out of each IKEA store each day makes running a logistics department an enormous challenge. A manager in this area drives the cooperation between the sales and logistics departments, knowing how to exploit every cubic meter of space. It is also the manager’s responsibility to supervise the ordering of products to the store, ensuring the correct quantities are acquired.
Where IKEA’s most innovative process comes from combining their retail and warehouse processes. Almost every store has a warehouse on the premises. This helps the company reducing transport costs. For example, imagine when someone selects a piece of furniture to buy. The item is then ordered, shipped from the manufacturer, moved from the delivery truck into storage in the warehouse, moved from the warehouse to the customer’s vehicle or delivered by the furniture retailer to the customer’s home. Every time the product is shipped, moved, and loaded, it costs money. IKEA does not have to do this as they all their products under one roof which is accessible to their customers
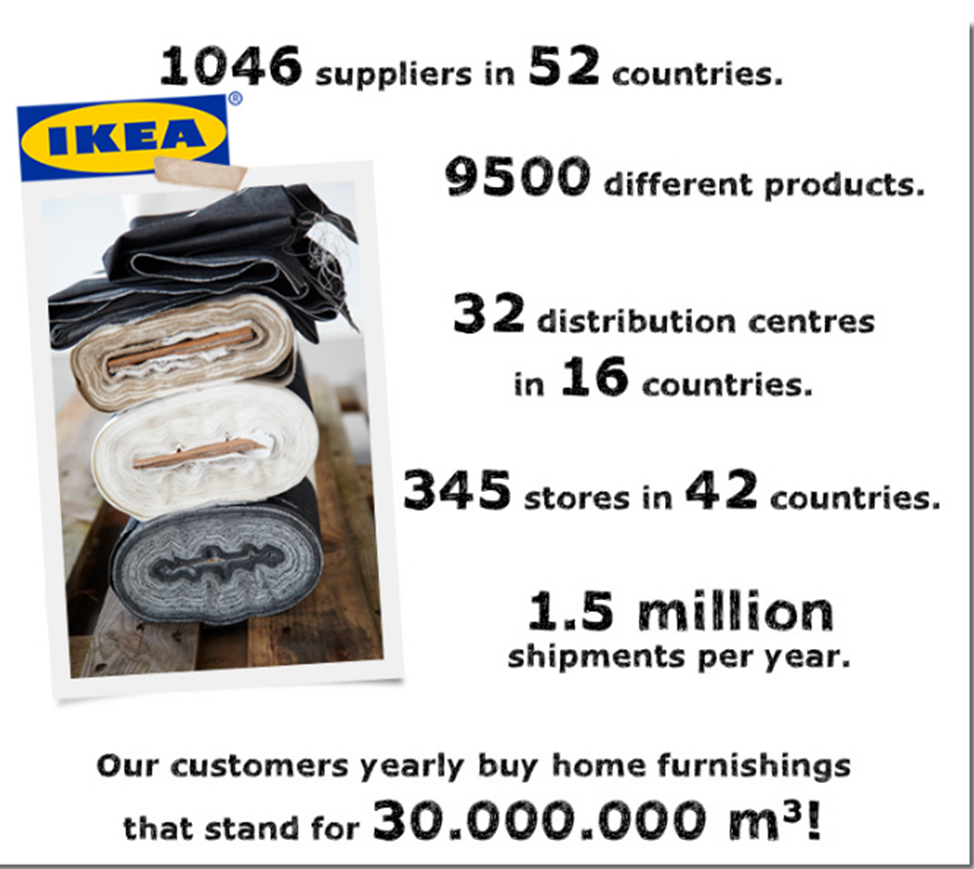
Sustainable Relationships with Suppliers
A key part of IKEA’s success is credited to its communications and relationship management with materials suppliers and manufacturers to get good prices on what it procures. Although Ikea fosters competition among suppliers to ensure they attain the best prices and materials, it believes in making long-term business relationships with them by signing long-term contracts, thus lowering prices of products further
IKEA is a very high-volume retailer – it buys products from more than 1,046 suppliers in 52 countries and uses 42 trading service offices around the world to manage supplier relationships. They negotiate prices with suppliers, check the quality of materials, and keep an eye on social and working conditions.
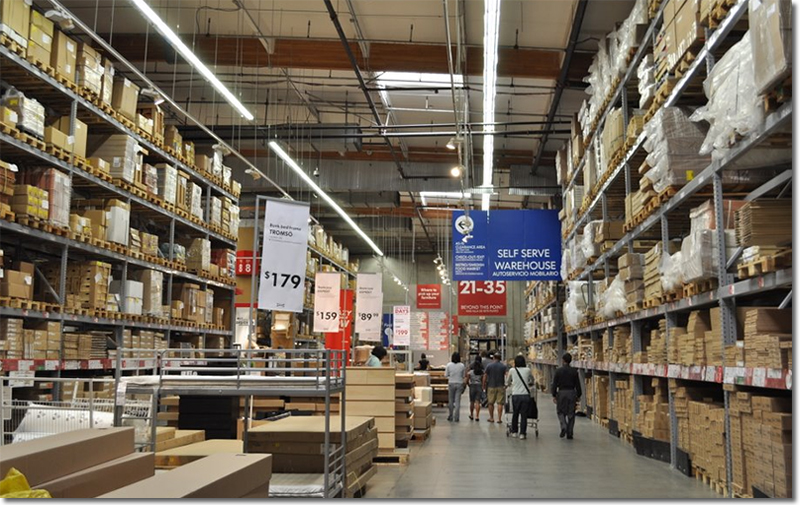
The duties of the logistics personnel are to monitor and record deliveries, carefully check delivery notices, sort and separate the goods, and get them off to the correct sales area or designated overstock locations. Overall, they ensure an efficient flow of goods within IKEA stores, which is essential to maintaining high sales and enhancing customer loyalty.