How To Keep Your Automated Trucks Running Smoothly
11th April 2024
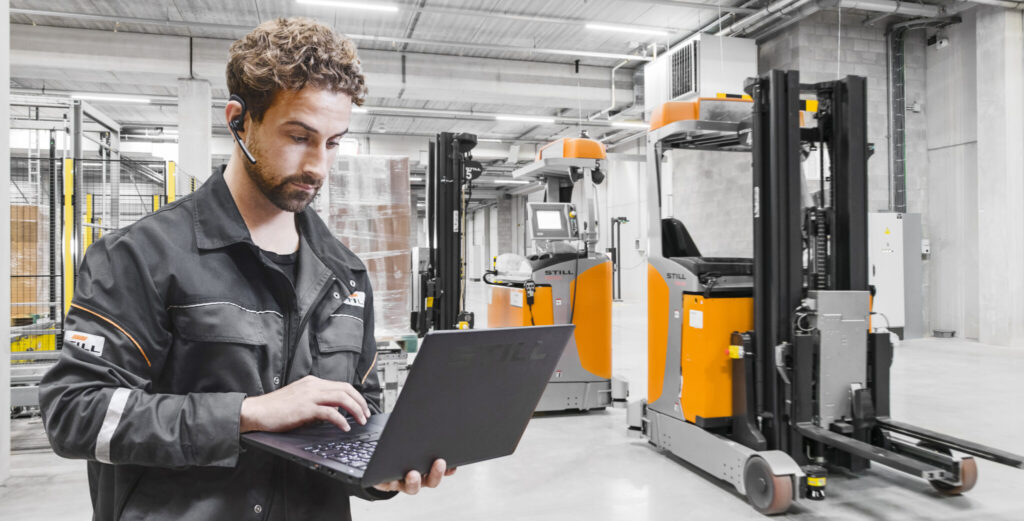
STILL, the Hamburg-based intralogistics provider, is systematically expanding its service concept and will soon be offering fast and flexible on-site service for automated trucks. In addition to the comprehensive service network and the expertise of STILL service technicians, a new digital service concept and, in particular, the use of standardised components will contribute to this. In addition, the centralised STILL spare parts supply ensures a high level of parts availability in the automation sector. With its smart, digital service concept, STILL is once again setting new standards in the industry.
Demand for automation solutions is booming – and companies are increasingly reliant on efficient solutions due to efficiency pressures, lack of skilled labour and growing global competition. However, even the best automation systems require regular maintenance and service to run smoothly and enable companies to realise the competitive advantages of automated solutions. This is where STILL’s experienced automation experts come in. Thanks to industrialised production and standardised components, STILL will offer a broad portfolio of automated vehicles with short delivery times and a wide range of customer-specific equipment options – and at the same time can further improve the speed and flexibility of service for automation solutions.
“When choosing the right partner, the efficiency of our systems is crucial for many of our customers,” explains Dr Florian Heydenreich, Executive Vice President Sales & Service STILL EMEA. “With this in mind, maximising the availability of our products in customer applications is a high priority, for example through fast and flexible service. Our customers have been acknowledging our excellent service quality for manual trucks for years. Now we can guarantee the same high standard for our first automated solutions.
The new concept is based on the industrialisation of both components and service processes. This enables the handling of automated vehicles to be comparable to that of production vehicles. Thanks to the standardisation of components and production, almost all spare parts can be ordered within a very short time from STILL’s central spare parts warehouse.
Digital twins and internal quality assurance tool to speed up service for automated vehicles
STILL creates a so-called digital twin for each automated truck in the company’s own cloud. If a component with software needs to be replaced in the event of a malfunction, STILL service technicians can quickly and easily configure new hardware with a backup from the cloud and install it directly on site. Compared to previous processes where hardware had to be ordered, centrally configured and then installed at the customer’s premises, the new STILL service concept significantly increases the availability of the trucks. Another advantage of the digital service concept is the integration of the automated products into the company’s internal quality assurance tool. Here, all service processes are documented and evaluated in a standardised manner. In this way, customer service experiences are incorporated into the continuous product optimisation process.
Reliable and personal: STILL’s comprehensive service network
The digital service concept also has a positive impact on direct customer contact. This is made possible by standardisation, a qualified training concept and a strong, nationwide network of service technicians. In other words, all service personnel will continue to receive comprehensive training on all products sold in their region and will be able to configure, implement, maintain and repair them – including automated trucks. This not only increases STILL’s service speed, but also strengthens customer confidence in the STILL brand. “With our smart service concept and the digital twin for our automated trucks, we are setting a new standard for fast and flexible service,” says Dr Florian Heydenreich, summarising the benefits. “We now need to extend this standard step by step to our entire automation portfolio”.
First impressions were given to visitors at this year’s LogiMAT from 19 to 21 March in Stuttgart. STILL presented the new EXV iGo high lift truck with digital service concept.