Let me profile a company – I have an actual company in mind, but this one is only a concrete example.
This company has been engaged with continuous improvement since at least 1998. Yet, just a few weeks ago, they posted an opening for a Continuous Improvement Director. And this isn’t the first time. I have seen this position posted by this company every couple of years.
The posting explicitly calls out this C.I. director’s responsibility to “champion” their “[Corporate Name] Business System.” That at least implies that the [Corporate Name] Business System is something aspirational that must be internally championed by others rather than the way they simply do business every day. Indeed, they feel the need to hire someone from outside the company to champion their [Corporate Name] Business System to their own leaders. This is pretty strong evidence that the actual Business System within the company is something radically different than [Corporate Name] Business System.
This is not a sign of success over the past quarter century. Quite the opposite. We have a company with people on the payroll who were not even born when the C.I. effort was initiated. If senior leaders have come up through the company ranks, they have been exposed to the tenants of the [Corporate Name] Business System their entire careers.
Yet it is still necessary for a dedicated person to advocate for it.
If this company might be you… here are some questions to think about:
How much actual cultural change has taken hold in the day-to-day operations since you have been engaging in kaizen activities?
Is the daily activity of your line leaders – the team leaders, supervisors, first line managers – reflective of something other than your [Corporate Name] Business System? If so, why? What forces are at work to push those activities in a different direction than the one you say you want? For example, are there metrics or line management expectations that run counter to moving continuously toward 1:1 production at takt? What policies or expectations are in place that systematically undo the results of a kaizen event?
How much daily kaizen is done by your line leaders? Your supervisors? Do your first-line leaders coach your supervisors on improvement? Are they qualified to do so? If yes, do those improvement activities tier up through line management toward the higher-level goals of the company?
Do your manufacturing supervisors have the basic industrial engineering skills? Can they fluently talk about takt time, cycle time, flow, work balance, etc? Are those skills represented in the way they run their day-to-day operations?
If the answers to these questions are largely in the negative — if you have been at this for two decades+ and they are still in the negative, then I think I can safely say that this isn’t just some kind of fluke. What you have been doing is not working. If you are looking to do more of what you have been doing, maybe consider trying something else.
That being said, don’t give up. It isn’t that this stuff doesn’t work, it is that your approach to embed it into the organization has, up to this point, been ineffective.
Consider an approach where the primary focus is on the patterns of day-to-day interactions between people, working toward having them engage in effective problem solving and learning on a daily basis. If improvement only happens as an event, then it is, by definition, not “continuous.”
I believe that structuring those day-to-day interactions is the purpose of all of the so-called “lean tools” (and all of the other “tools” called out by other packages such as TQM, xSigma, TOC, etc). But unless those tools are deployed with that purpose in mind, it is all too easy to put in the mechanics without creating any shift in the culture.
And it is the culture that actually matters.
So ultimately my question is this: Do you have the continuous culture that you want today? If your [Corporate Name] Business System is actually in place, congratulations. But if that culture is still aspirational, and if you are trying to, yet again, hire someone from outside to champion that culture, what is everyone in charge doing?
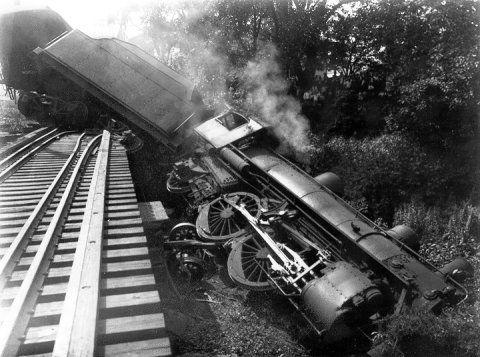
https://playingintheworldgame.files.wordpress.com/2013/09/17082-strip-zoom.gif
Mike, really great, LOL. Why are you looking and posting at 4AM??
Don’t answer, juxst change, Unless you were in Europe !
Mark,
Seems to me you might have missed a key item. They don’t have the culture to effect change. Perhaps they are just checking the box that that should have a CI group and need someone to lead it, but not really change it….
Pat – good point. The question “Why are you doing this at all?” is one that I should have asked here.
I hit on the same topic about a decade ago here: https://theleanthinker.com/2013/11/10/learning-to-see-in-2013/
Mark,
Thanks for your reply and the link to the ‘old’ post.
I liked it. Didn’t know you then, I was busy having done VSM’s as a consultant at many places. I had had a ‘revelation’ when I read LTS and had wished I had seen it a long long time before. Thought it was a great way to see! In 2011-12 Conrad Soltero and I had read Toyota Kata, and knew we had to learn more. We were pleased to be able to take Mike’s course on TK in Michigan and meet and talk with him. We also came to the realization, then, that TK had huge similarities to TWI, which is why we wrote the book “The Seven Kata; Toyota Kata, TWI & Lean Training. Since then, slowly, but surely the 2 became intermixed in many ways.
You of course, are correct that in attempting to do a VSM, one must have and end in mind and move towards that point. You also point out one interesting item that many people don’t seem to recognize that the potential Kaizen bursts should be on the future state map, I personally think that partly it is when doing the current state, something ‘graphical’ needs to be done on the current state, to communicate where an issue exists. Especially to management.
What’s worse is that they’ll probably require some sort of Six Sigma or lean “certification”.
Certifications – see my thoughts from 2008 here: https://theleanthinker.com/2008/06/18/certifications-buying-credibility/
And I have learned a thing or two since I wrote that. Even though I use Japanese jargon in that post, time has passed and these days I use almost none unless the company already has that language embedded into their culture. Today if I hear a heavy jargon dump, that is indicator for me to check a little deeper for actual credibility.
*smile*
Just to clarify, it isn’t a sign of success if you are *still* looking for an outside “champion” after being at it for 20+ years.