Digitalization Efforts you can count on
26th September 2023
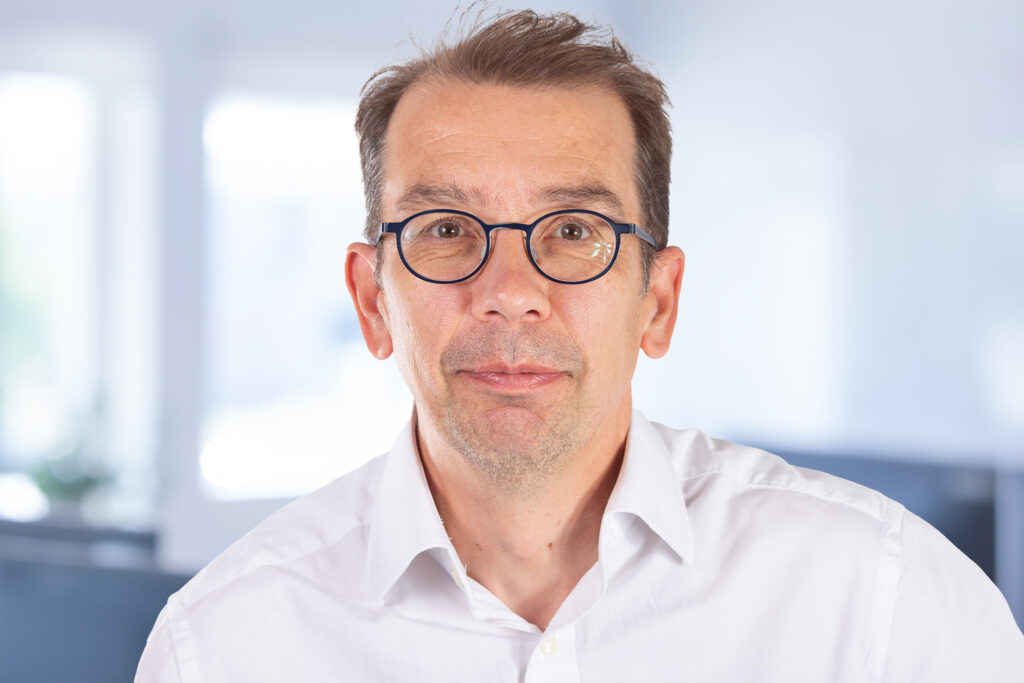
According to a recent report by MHI and Deloitte (1), 74% of leaders asked were looking to invest in supply chain technology and innovation. But how certain can you be about payback times, and how much disturbance will implementing these projects cause? Are there technologies that are easy to implement yet give instant ROI?
The report found that many companies were investing money in several areas of their supply chain operations, specifically warehouse and network optimization, sensors and automatic identification, robotics, and artificial intelligence. The desired outcomes are obvious; reduce costs, increase operational efficiency, improve customer experience, and as a result, reduce climate impact on receiving and delivering goods.
Digital transformation – what’s the problem?
One presumes that logistics managers see digital transformation as moving from analogue to the digital world to become more dynamic and adaptable to a fast-changing environment. But projects put logistics managers under pressure. The worst-case scenario is spending millions while not reducing expenses, gaining the expected efficiencies or reaching required revenue goals. For example, problems may be related to barriers against sharing data, the complexity of underlying processes and systems, conflicting interests or resistance to change.
Donald Houben, Head of Sales Europe at SiB Solutions, puts it like this, “Innovation projects add extra strain on workload for logistics managers especially when operations suffer from processes that are inadequate, or where change management is not properly in place. But there are digitalization projects that can quickly and easily harvest low-hanging fruit.”
His colleague Paul Bowes (pictured) , Technical Project Manager at SiB Solutions, agrees: “Lack of visual insights and visual proof hinder continuous improvements as the wanted KPIs and statistical measurements are difficult to quantify. Companies see this by using Intelligent Video and AI Services. In one instance these insights showed that up to 40% of assumed picking errors were not actually picking errors(2)”.
So how do you go about digitalization, and what do you want to achieve? One answer is to implement subscription services that can be ready in just a few weeks after commissioning. An example is Intelligent Video and AI Services that make it easy to visually search for goods and immediately see the answer to where they are and their condition in any situation.
The benefits of subscription-based Intelligent Video and AI Services
Subscription-based services help eliminate up-front costs, offer instant updates for upgrades, are often modular, enabling organizations to take what they need and add on later, and give companies complete financial control as fees are set.
When companies implement intelligent Video and AI Services, logistics professionals can quickly go back in time and see every event, from inbound, throughout the picking and packing process, to dispatch. Visual insights help to quickly resolve disputes by verifying claims and giving proof of exactly what was received, picked, packed and dispatched. The positive financial implications are obvious. So too are the positive effects on personnel.
Intelligent Video and AI Services are key to improved quality, less errors, happier customers, and ultimately higher margins. It protects companies from fraud related to inbound logistics and returns. In other words, a transformation project you can count on. Literally.
(1) The responsible supply chain: Transparency, Sustainability and the case for business. MHI and Deloitte.
(2)SiB Solutions: https://www.sibsolutions.com/save-money-by-getting-rid-of-pointless-claims-investigations/