Core System Optimisation Vital Link for Supply Chain
14th May 2024
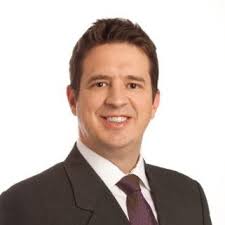
Core system optimisation is a vital link for manufacturing’s supply chain success, writes David Lees (pictured), CTO of Basis Technologies.
Manufacturing supply chains are growing increasingly complex and difficult to manage. Factors like nature-related risks, geopolitical dynamics and business transformation have decreased the resilience, availability, and viability of managing supply chains effectively. However, one of the key barriers to supply chain success for global manufacturers is the archaic state of their core business systems, such as ERP.
ERPs, such as leading provider SAP, is the beating heart of many logistics organisations yet is often overlooked by CIOs. It’s widely regarded as being a ‘constant’ in and amongst business innovation happening around it – it’s the age-old foundation that has kept the company running for years. However, what CIOs may be unaware of is that these established systems have become ticking time bombs. As the ECC support deadline in 2027 grows ever closer, the race is on to prepare SAP systems for a mandatory transformation toward the cloud-based S/4HANA in time. And since these operations sit at the heart of the tech stack, the collateral damage of falling or ignoring the need for transformation altogether is substantial.
SAP itself recognises that many businesses are pushing their legacy systems to the brink, just in an effort to manage day-to-day operations across their supply chain. There is an industry-wide call for a way to unify, connect, and coordinate their supply chains more effectively and unlock the full potential of data-driven decision-making.
As a result, optimising these core systems is no longer a luxury for manufacturers; it’s non-negotiable.
Don’t shy away from change
The idea of making substantial changes to such a deep-rooted business system has put organisations off for years. Fear of unexpected costs, human error and operational collapse have been reasons enough to warrant holding off making any major alterations to such a central asset like SAP.
However, it’s now reached the stage where doing nothing is equally, if not more, damaging in the long term. It’s time to get rid of the ‘if it ain’t broke don’t fix it’ attitude, particularly considering the competitiveness of the manufacturing landscape worldwide.
Untold benefits await those manufacturers that move away from this mindset. If they can transform their legacy systems into platforms for innovation and growth, manufacturers can unlock huge value, including improved efficiency, increased customer retention, reduced overhead and operational costs, and fewer IT issues in general.
However, the way in which these core systems are managed in the manufacturing space currently act as a significant roadblock to these benefits. The problem is methods of change often lack the capabilities to capture the insights needed and match the pace of the organisation. It’s like trying to navigate a storm without a compass – a recipe for disaster in the world of supply chain management, particularly as manufacturers negotiate a consistent stream of CSR mandates when it comes to supply sourcing and manufacturing practices. According to the Business Continuity Institute’s 2023 Supply Chain Resilience survey, concerns about new laws and regulations increased by 40.5%, representing the fifth biggest concern for organisations.
Moving beyond a manual approach
Manufacturers with complex supply chains have large SAP environments, which is all the more reason to move away from archaic ways of managing these core systems. Basis Technologies recently found 59% of enterprises still uses manual Excel spreadsheets for business-critical SAP management. This is at odds with manufacturers’ vision for the future; Deloitte research from 2019 stated 83% of manufacturers believed that smart factory solutions would transform the way products were made in five years. Five years later and little has changed, as the lack of core system optimisation continues to impede progress across the operational funnel.
Spreadsheets are firmly rooted in the years that came before, and no longer meet the demands of modern businesses. Technologies such as automation, machine learning, and AI have enabled businesses to act smarter, leveraging data analytics and efficient technology to manage their operations more thoroughly and with increased ease.
To effectively manage change within SAP systems, organisations require a more robust approach: an automated system where everyone has a clear view, can work together seamlessly, and can take action instantly. This requires real-time visibility, collaboration, and integration. By replacing manual spreadsheets with automation, manufacturers will unlock real-time impact analysis, adaptive governance, automated backout and landscape flexibility, across the entire supply chain. CIOs are aware of the need for innovation, but progress has been hindered by tools ill-suited for the task.
By taking back control of SAP systems, manufacturers can gain a holistic view of their supply chains, acting on data-driven decisions to inform more sustainable practices, eliminate supply chain disruption from human error-driven IT outages and integrate SAP systems with their IT stack. Ultimately, this is the way manufacturers future proof their business.
The time for change is now. By embracing modern technology for core system optimisation, manufacturers can cultivate a more resilient, efficient, and sustainable supply chain. This, in turn, unlocks a domino effect of benefits, from improved customer satisfaction to reduced costs and an edge in a fiercely competitive market. The future of successful manufacturing supply chains lies not just in the new, but in leveraging the full potential of the technology that already exists within the heart of the organisation.
read more